Active marine terminals are busy, with multiple disciplines working alongside each other daily. For owners, safety is the highest priority. When remediation work is necessary, a successful contractor must demonstrate a very high level of internal safety training and well-disciplined site personnel.
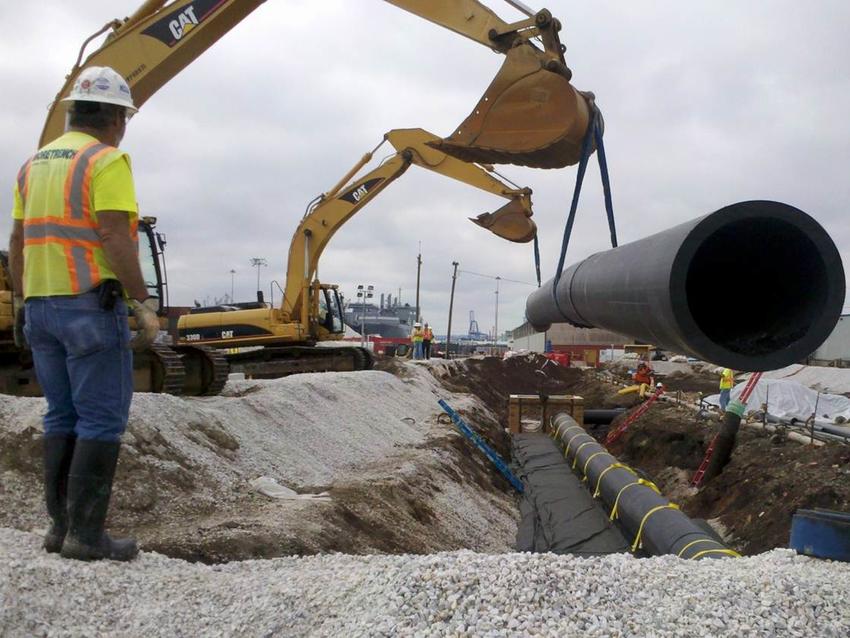
The project
Over several years, a petroleum-based contaminant seeped into an existing concrete storm drain and open drainage swale at a Baltimore, MD terminal. The contaminants originated from long-term leakage of underground pipelines. Concern that the contaminated surface water would reach the Baltimore Harbor led to a permanent solution mandated by the Maryland Department of the Environment. Given its safety program and record and ability to accomplish all aspects of the work under one “umbrella” contract, Moretrench Industrial was awarded the contract, drawing on expertise from sister companies to ensure the highest quality end product.
The challenge
A primary consideration was ensuring that work did not impede the busy terminal’s bulk goods and material storage and haulage operations. In addition, crews needed to address specific challenges associated with the overall work:
- The terminal was built on urban fill placed to create useable land. Numerous obstructions within the fill included wood, steel, slag, barrels, railroad ties, and concrete, which required extra care during the excavation process.
- The soil contaminants were potentially flammable and explosive. The typical fusing of shorter pipe sections within the excavated trench was abandoned in favor of remote section fusion, with long (100+ ft) lifted and set into the excavation in one piece.
- The pipe sections had to be bedded and anchored in a concrete slab to prevent them from “floating” after backfilling was completed, and dewatering discontinued.
- Sheet pile shoring along an existing warehouse could not be used due to potential vibration-induced damage to the building. Therefore, sonic drilling methods were used to install pilings, with road plates behind the pilings to retain the soils.
The solution
Moretrench Industrial’s work included excavating 1500 LF of pipe through petroleum impacted soils, installing 3500 LF of HDPE pipe and 16 concrete drainage structures, and constructing a 110-ft concrete channel outfall. The overall scope of work also included off-site removal of over 25,000 tons of contaminated material and replacement with clean backfill; dewatering and treatment of petroleum-contaminated groundwater; and complete restoration and repaving of over 16,000 SY of asphalt pavement.
Despite these challenges, Moretrench Industrial completed all aspects of the remediation program in a little over a year.